We’re big fans of Van Son for letterpress ink: it has an intense color strength; it’s consistent; and it’s quick setting. That’s why we use these inks exclusively in our own print shop. We offer two ink types, both well suited for letterpress. Use rubber-based inks for general letterpress printing—it’s the type of ink we use every day in our shop. Use the oil-based inks if you’d like a glossier ink that works well with coated papers (though you won’t be able to leave the ink on press overnight). (read more about how to choose the right letterpress ink)

Examples of letterpress in a Sentence Recent Examples on the Web Most of the products are manufactured in-house across six studios that specialize in areas like letterpress printing, monogramming, and embroidery, along with a manufacturing kitchen. We have 60 free Letterpress Fonts to offer for direct downloading 1001 Fonts is your favorite site for free fonts since 2001.
- Letterpress papers are uncoated and mostly or all tree-free (cotton, bamboo, and combinations). We recommend the following paper mill brands: Crane’s Lettra, Mohawk Strathmore, Holyoke Cotton, Rives BFK Cotton, Reich Savoy Cotton, Legion Bamboo, Revere Cotton and Somerset Cotton.
- That’s what we hope we give you every time you open a bottle of Letterpress spirits and take your first sip. And your second. It’s what we share with you because it’s how we do things. From the first step through each part of the process, every batch we make. We hope you enjoy each sip you take as much as we enjoyed making it for.
View FAQs
The attractive letters pressed onto business cards, birthday greetings and wedding invitations might seem like everyday inscriptions, but these precious words have a meaningful history. While we keep these items as reminders of big events or people we’ve met, keep in mind that each letter was created with a great deal of care.
Letterpress printing is also known as relief printing, and it is the earliest form of printed language in the modern world. By combining ink, paper, a strong push of pressure and a great deal of skill, the first words were inscribed this way thanks to the Chinese in AD 175.
The practice may be simple, but the tradition is deep. Here, we’ll take a look at the history of letterpress and how it transformed into what is considered a modern day art.
AD 175: Chinese Woodblock Printing
Perhaps the oldest known form of letterpress printing was that used by the Chinese. Early findings show that wood printing likely began in the eighth century as a way to record history, as well as share the message of Buddhism.
During the letterpress printing process, calligraphers would complete up to four proof readings for one printed item. Inscriptions carved into a block could be corrected with cutting small notches in the lettering and shoving in new pieces of wood. If larger errors needed correcting, the calligrapher would create an inlay. When the block was finally perfected, it was washed and fresh ink would be applied.
Wax paper placed on top of the block would be rubbed with a pad to transfer the inscriptions onto the page. The letterpress prints found during excavating were made in red, blue or black ink, and an experienced pressman could make up to 1,500 copies each day.
1440: Welcome the Modern Day Printing Press
Woodblock printing was commonly used from the eighth to the fifteenth centuries, until a German man named Johann Gutenberg invented the printing press in the early 1440s. Gutenberg wanted to find a way to supply books to the common person – a huge step in print press history.
The letterpress process of carving entire pages onto blocks of wood was tedious, and left little room for error. In his early days of printing, it’s believed that Gutenberg started carving individual letters into pieces of wood. These letters could be used over and over again, formed into a variety of words and then rearranged for the next page. This version of the printing press was the earliest form of moveable type, and a huge advancement in the history of letterpress.
But Gutenberg found the wood easily became worn down, rendering it unable to print clearly. In hopes of finding a solution, Gutenberg started working with metal.
He started using steel to create capital and lowercase letters, as well as punctuation symbols needed to create a complete text. Keeping up with his inventive spirit, Gutenberg created his own ink out of soot, turpentine and walnut oil to transfer the letters onto the page.
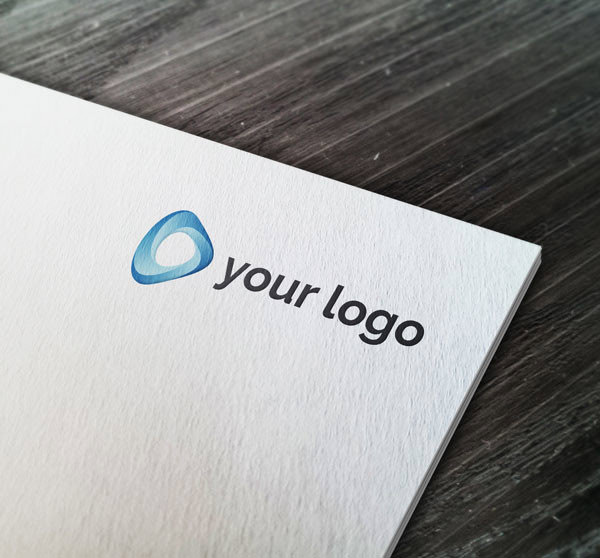
This early form of the printing press was known as a “screw press.” By the time Gutenberg’s press was fully operating, he was printing six pages per day. One of his most impressive accomplishments was printing the Bible. Two volumes of the Bible had 1,282 pages and required about three years for his staff of 20 people to complete. Gutenberg made about 200 copies of the Bible during his lifetime. About 48 can still be viewed in museums.
1473: England Joins the Movement
William Caxton was the first Englishman to get his name in the books of England’s printing press history. After observing the growth of printing in Germany, Caxton wasted little time in setting up shop in Bruges, where he printed the first book in English.
When he returned to Westminster, he continued printing, putting out the first copy of Chaucer’s “Canterbury Tales,” one of the most famous works of English literature. His work is believed to be one of the earliest attempts to standardize the English language, and many of the works he produced became popular to the upper classes of English society.
1706: The Style Alters
While Gutenberg’s original printing press changed very little over 350 years, one Englishman sought a way to improve the process. John Baskerville, a printer, papermaker and typographer, printed items for the University of Cambridge.
The style of his print was popular because he developed a whiter, brighter paper that better showcased the black ink. He also started using wider page margins and implemented a lead before each paragraph.
1798: Lithography Printing Steals the Spotlight
Lithography printing was invented by Alois Senefelder as a way to improve the process. This type of printing made it so that the entire page, including the text and the white space, could be on a single printing plate.
Lithography also turned out to be more affordable because of cheaper paper. Also, because it was run by steam, the lithography printing process produced more pages than letterpress printing. With the invention of lithography printing, printers started using color. Within the next century, lithography would become one of the largest forms of printing advertisements and magazines.
The introduction of lithography didn’t stop the letterpress from making a strong move forward in the 1800s. The jumpstart of the Industrial Revolution helped the letterpress continue to improve. First, the leverage and weight was adjusted to create more even pressure. The invention of a tabletop press allowed for more clarity in each impression thanks to a longer side arm that gave more leverage. Smaller tables also became popular in smaller businesses, where just about everyone could do their own printing.
Larger presses that were previously run by someone pushing a foot pedal while hand-feeding paper into the press were now run by motors. As the technology advanced, presses soon became motor-fed, leading production to boom up to 5,000 copies in an hour.
Late 1800s: Linotype and the Newspaper Industry
One of the first improvements to lithography came in 1876. A young German man named Ottmar Merganthaler was working in Baltimore when he was asked to fix a machine intended to do both the work of typewriting and lithography.
The machine had been invented by James O. Clephane and although it never caught on in the printing industry, the ideas helped Mergenthaler improve the use of casting. The two worked on a machine that would punch letters through papier-mâché. Despite Mergenthaler’s suggestions that it wouldn’t work, the pair kept at it. The machine was abandoned after his concerns proved true.
Mergenthaler completed a machine in 1884 that proved to be the first form of linotype – a system that produced a single line of type in one motion. This was known as a “line casting” machine. Similar to a typewriter, someone would select letters on a keyboard and a small band of paper would be produced. The band fed into a machine that decoded the message and would cast the type using hot metal. If an error was made, the entire line would have to be retyped and run through the process all over again.

Mergenthaler soon realized that brass would produce better results, so he began working on a new machine. When it was released in 1885, it was a great success. With strong financial support, The Mergenthaler Printing Company was formed. The New York Tribune accepted the first machine and used it produce some of the paper in 1886.
The use of the machine boomed in the newspaper industry. Mergenthaler would constantly improve the machine, adding nine patents to its production. Control of the business moved into the hands of newspaper gurus who saw their own production of newspapers grow through the use of the press. They wanted more presses to be created as quickly as possible, but Mergenthaler wanted more time to create additional improvements. He was denied his request and forced to try to create a brass machine in huge quantities with steel punches – all of which had to be made by hand.
Letterpress
The work was overwhelming; Mergenthaler resigned in 1888. He later died of tuberculosis at age 45. Long after his death, the machine he invented would continue to transform the newspaper industry. By 1901, 8,000 machines were used by newspapers across the country. In 1954, it had grown to 70,000.
1870: The Platen Press in the United States
The platen press was designed by George Phineas Gordon in the late 1870s. He claimed that Benjamin Franklin appeared to him in a dream and told him to create the “turnover” press, which allowed for movement of the platen.
Although Gordo can take credit for selling thousands of presses in his lifetime, most of them were created by other people in machine shops. Gordon would eventually build his own factory in 1872 in New Jersey. In this building, he was able to make 600 presses each year.
The platen press is similar to letterpress printing and can even be found in small, amateur printing businesses throughout the nation. Platen presses created by Gordon’s predecessor, Stephen Ruggles, can be found in the Smithsonian collection. One has even been used for printing in the past few years.
1903: Offset Printing and the Modern Age
While historical forms of printing were developed over decades of research, offset printing was an accident discovered in 1903.
Ira Washington Rubel was using is lithograph press when he forgot to put a piece of paper inside the machine. The stone plate pressed the ink into the rubber that was used to make the impression. After he slipped the paper inside, Rubel found that the print from the stone transferred to one side and the ink on the rubber transferred to the other.
Wedding Invitation Letterpress
The print from the rubber was much clearer than that from the stone. Rubel would tinker around with creating a machine based off of his accidental discovery, but it took some time before offset printing would catch the attention of others in the industry.
Offset printing finally started to gain popularity, as it could transfer print onto paper, as well as metal and wood. Nearly 50 years after its discovery, offset printing had become the most popular form of press work.
1980: Photopolymer and the Digital Age
In the 1980s, photopolymer plates swept into the printing industry. Digital technology allowed a photo negative to be transferred to a printing plate, making it possible for printers to complete larger jobs, while smaller printers still used the time consuming practice of typesetting. This digital-forward technique allowed the practice of letterpress printing to find a new platform in the modern age.
Today: The Revival of Letterpress
As personal computers became more common in homes, printing could now be done by anyone. But some printers still desire the quality and feel of letterpress printing. When popular companies released invitations with deep, letterpress type, it sparked a revival in the letterpress industry.

Historical letterpress printing barely touched the paper before transferring the ink. It was a practice known as “kissing” the page because if it’s light, gentle look. Today, letterpress is known for the deep indentations it leaves behind. This technique is known as “debossing,” and leaves no question that it is authentic letterpress printing. This style pushed letterpress printing to be considered a modern day art.
While offset printing is still popular in professional businesses and home printer projects, letterpress is a craft that takes skill, patience and time to create. People don’t just want words on a page. They demand quality, and the look and feel of paper is often only achieved with the practice of letterpress printing.
Gutenberg’s original design of individual letters can still be found in some printing shops, but modern advances now make it easier for printers to accept the convenience of the digital age while keeping the look of letterpress.
Technology allows artists to design a digital page and transfer it to a photopolymer plate. These plates are then pressed into the paper, replicating the same look and feel of traditional letterpress with a colorful, artistic touch.
Letterpress printing made a big comeback with wedding invitations, which can be as simple or ornate as the customer wants, complete with custom envelopes, location maps and reply cards. Letterpress printing also covers numerous aspects of the wedding process, including save-the-dates, place cards, programs, coasters and menus.
But letterpress printing goes beyond wedding planning. Share the good news of a birth announcement on memorable, unique cards. Party invitations for showers, bar and bat mitzvahs and birthday parties are also a popular keepsake for letterpress printing.
More formal letterpress options are found in business cards, custom stationary and gift tags. Many businesses also have found letterpress printing gives a unique, custom feel to posters and even in QR codes that send people back to a company’s website. Paper also has adapted to the art of letterpress printing, as they are now available in thicker cardstock that can withstand the pressure. Letterpress printing provides a quality product that welcomes the viewer to touch the fine ridges that create a one-of-a-kind image.
The Future of Letterpress Printing
As technology continues to streamline the printing industry, artistic print designs grow in demand. Digital printing has even helped bring new life to letterpress printing thanks to the first 3D letterpress font produced in London.
Known as the “second industrial revolution” in the printing world, 3D-printing allows accuracy to rise to new levels. Typeface designers Scott Williams and Henrik Kubel designed A2-Type Foundry and use the advances of 3D printing to take the glory days of letterpress printing into the future.
Locust St. Press
Look to the time-honored practice of letterpress printing the next time you need business cards, invitations or simply want a decorative piece for your home or office. Let Locust Street Press provide you with a print that will leave a lasting impression.
Sources:
1. http://www.artisanpress.com.au/index.php/en/2012-03-13-04-59-14/letterpress-history
2. http://en.wikipedia.org/wiki/History_of_printing_in_East_Asia
3. http://elationpress.com/resources/the-history-of-letterpress-printing/
4. http://www.bpsnet.org.uk/history_print.html
5. https://letterpresscommons.com/merganthaler-linotype/
6. http://www.hrc.utexas.edu/educator/modules/gutenberg/books/printing/
7. http://thebeautyofletterpress.com/letterpress/
8. http://www.atypi.org/events/2018make-to-the-future2019-london2019s-first-3d-letterpress
9. https://letterpresscommons.com/platen-press-history/
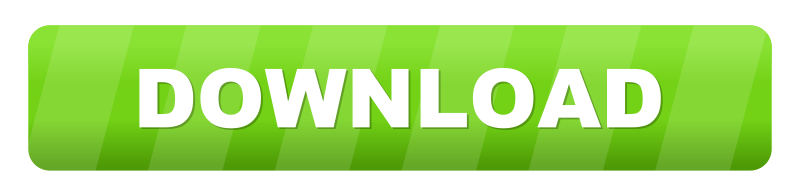